The life sciences sector is instrumental in advancing healthcare quality through the creation of new medicines and tech-advanced medical devices that enhance patient care and outcomes. It is crucial to maintain a clean environment in laboratories, cleanrooms and production areas where new medical devices, vaccines, drugs and other pharmaceutical products are researched and developed. This ensures the protection of critical pharmaceutical processes, equipment, staff and ultimately the final product.
One key facet of maintaining a clean and healthful environment is ensuring an uncontaminated air supply. According to Food and Drug Administration (FDA) data, contamination was by far the leading cause of medication recalls in the U.S. in 2022 and 2023.1 This statistic highlights the importance of clean air in the life sciences and emphasizes the crucial role of air filtration in preserving the safety and quality of pharmaceutical products.
Most global specialists in the life sciences industry use Camfil HVAC air filtration solutions in cleanrooms, production areas, and laboratories. These solutions help to create and maintain a steady flow of clean air in the process chain. They effectively control contaminants from various sources, addressing air quality issues in different settings, thereby reducing risks for workers and processes, and aiding compliance. Using these products also helps reduce operating expenses by decreasing energy usage and equipment downtime.
Fundamentals of Air Filtration in Life Sciences Facilities
Air filtration systems are crucial for maintaining facilities that meet high standards of hygiene and air quality. The rooms in the facility are isolated from each other in order to allow for the particle levels in each room to be controlled independently, with no contamination between rooms. Those rooms where cleanliness is critical, since they are closest to where the drugs are manufactured, are referred to as “cleanrooms.” Cleanliness levels are specifically defined by a classification system such as ISO 14644.
In a typical indoor setting, such as an office space, for example, the air might contain over a million particles per cubic foot.2 A typical pharmaceutical cleanroom, by contrast, would allow a maximum of 10,000 particles per cubic foot (ISO 7 classification) or even 100 particles per cubic foot (ISO 5 classification).
All air entering a cleanroom must be filtered with a HEPA-grade filter immediately prior to entering the cleanroom. Note: A HEPA filter is a particulate air filter and is classified as such under one of three globally recognized test standards: IEST RP-CC001, EN-1822 or ISO29463. This is typically done in ceilings of the cleanroom and is referred to commonly as terminal air filtration. Terminal filters are the last line of filtration, immediately prior to the cleanroom, as shown in the figure below.
Terminal filters must meet rigorous standards since their quality and performance are critical to the protection of products (pharmaceuticals), people and processes inside the cleanroom. Pharmaceutical manufacturers trust Camfil, more than any other supplier, to manufacture and deliver their terminal HEPA filters.
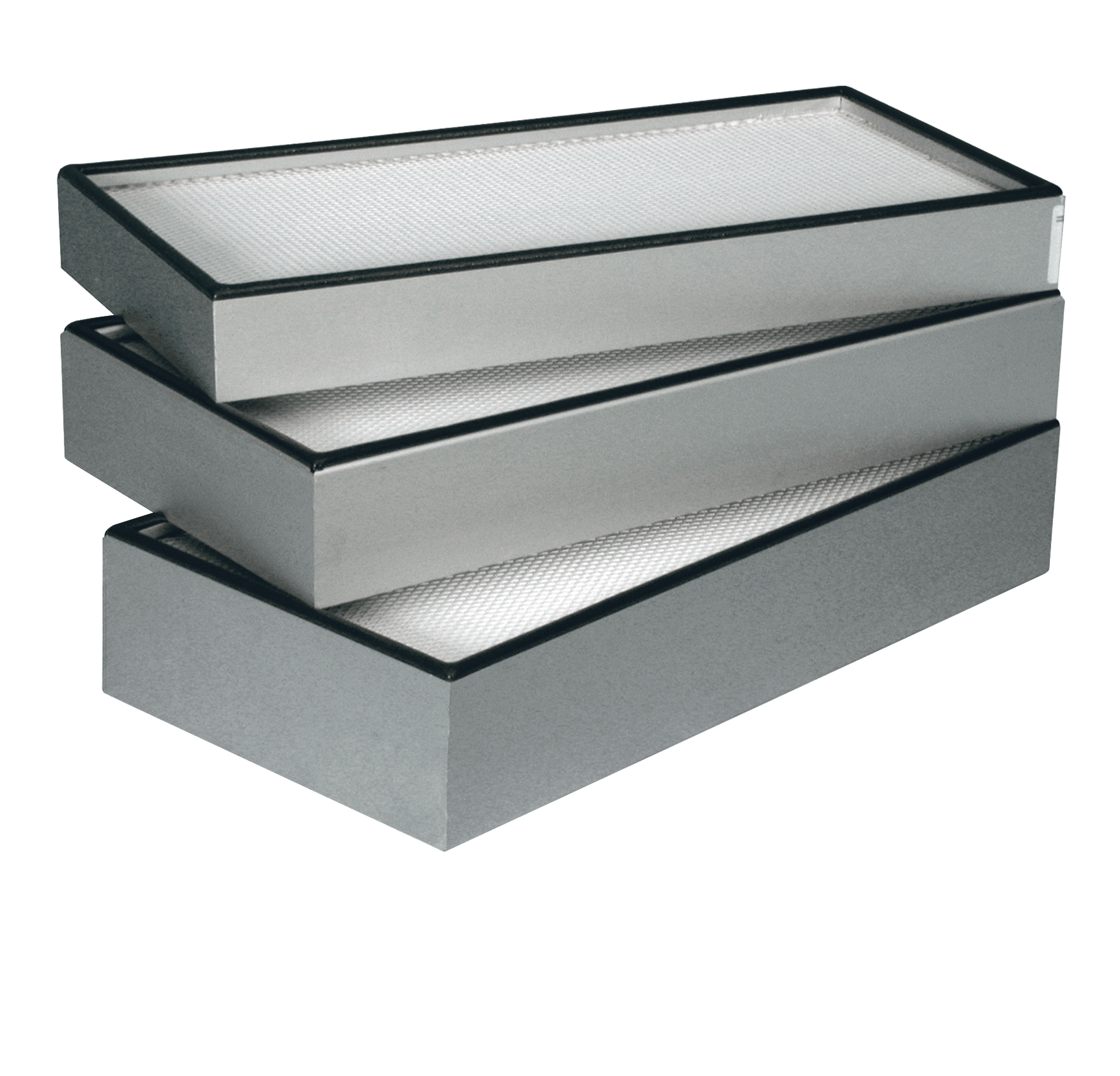
This Camfil Megalam® panel filter is an ideal HEPA/ULPA-level replacement for most cleanroom filters, housings and ceiling modules and grid systems.
Also important are other filter components of the facility’s air filtration system. There are often two or more stages of filtration upstream of terminal filters in the air handling units (AHU). AHU filters are critical to prefilter the air, removing large particles that would otherwise contaminate the HEPA terminal filters prematurely. AHU filters should also be made with minimal resistance to airflow in order to minimize the fan energy consumed by a facility.
Exhaust filters are typically found near the floor of the cleanroom, filtering the air before it exits the room. The exhaust filters help to direct the flow of air in the room and ensure that potentially harmful substances and organisms are removed from exhausted air.
The filters themselves are critical, but the housings that hold the filters are just as critical. Camfil housings are designed to integrate with the facility’s ductwork. They create a leak-free seal in order to ensure air goes through the media of the filter and no foreign material enters the ductwork. Units such as the Camfil PharmaSeal® terminal filter housing (shown below) are offered with customizable product features, as specifically requested by the pharmaceutical industry, such as room-side access for filter changes and filtration efficiency tests.
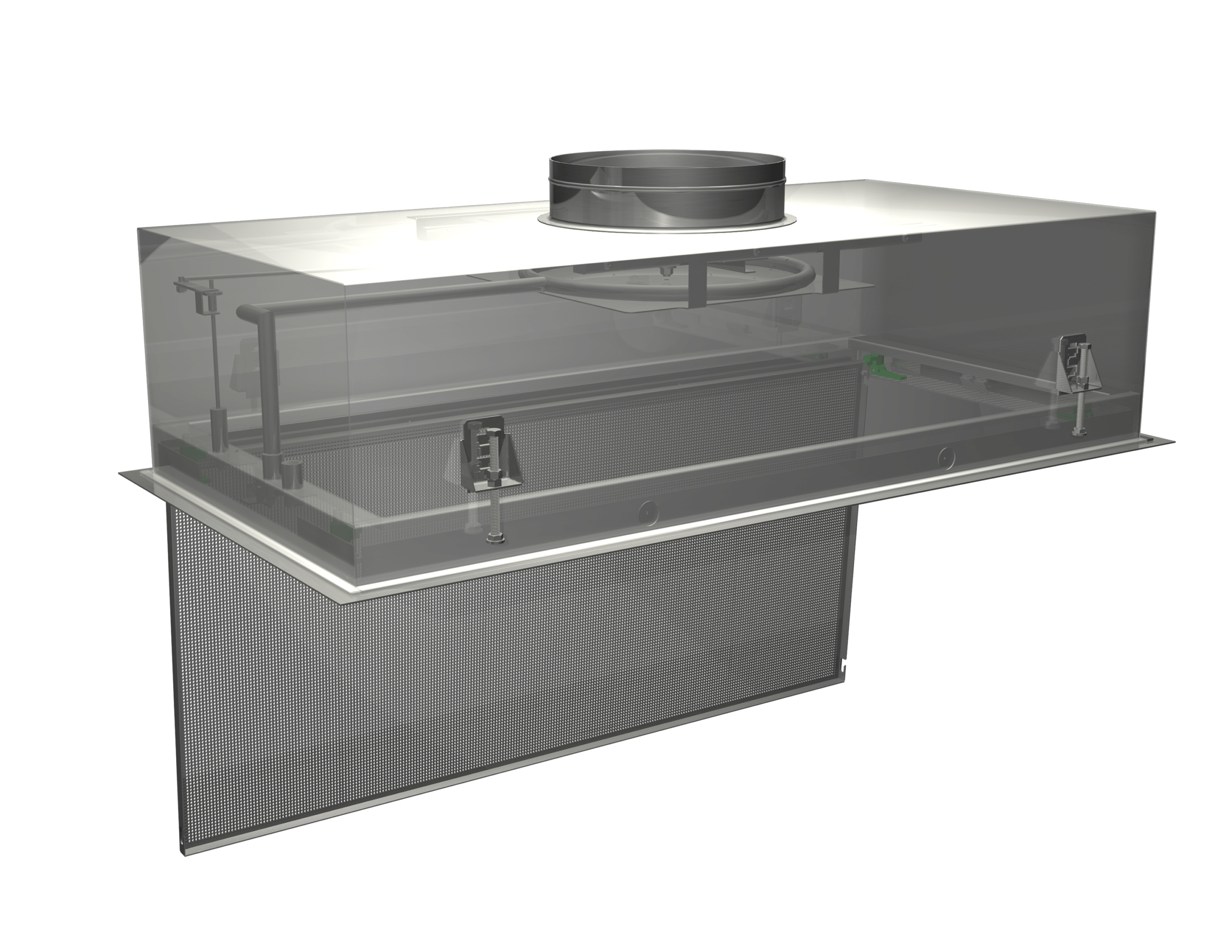
The Camfil PharmaSeal® terminal filter housing is offered with customizable product features.
Life sciences companies will use other filter technologies and strategies such as source capture devices, dust collectors and molecular (carbon) filters to control airborne contaminants, particulates, dust, odors, gases and pathogens throughout their critical facility areas. When added to existing HVAC systems, suitable filters can safeguard not only individuals, products and processes but also reduce energy usage and ensure compliance with regulatory standards concerning cleanliness levels. By implementing all these strategies, you can reduce the risks posed by airborne contaminants to costly, sensitive equipment, product quality and worker safety.
Different Air Filtration Needs for Different Drug Products and Processes
Pharmaceutical manufacturers often require varying filtration products and methods, depending on their product form and/or specific drug formulation. Some are challenged with the removal of solid dust particles that come from the product they are producing, such as a powder that is pressed into a pill form. Others may be making a liquid drug, supplied in a sterile glass vial, which gets filled inside process equipment on the production floor. Air filtration remains essential in all manufacturing scenarios to uphold a clean environment characterized by superior indoor air quality.
Dust Particle Extraction and OSD Processes
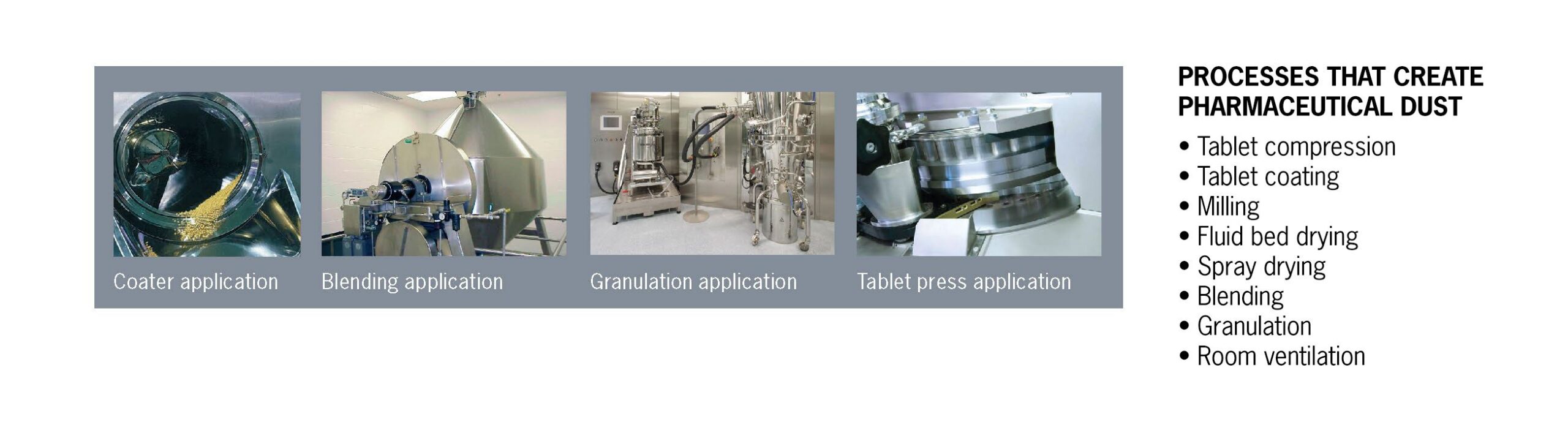
Pharmaceutical processes can generate dust that is potentially hazardous to operations and staff, and in any case will cause process variation if it becomes airborne. Dust collection systems are specifically designed to remove this airborne dust.
During the production and packaging of oral solid dosage (OSD) products like tablets, pills and capsules, dust can be generated from granular ingredients such as powders. Manufacturing and processing active pharmaceutical ingredients (API) often generate very fine, concentrated dust. The presence of very fine pharmaceutical dust is a significant concern because it can threaten worker health as the particles can be inhaled and lodge in the lungs. Furthermore, dust can have explosive properties.
Airborne dust can also cause cross-contamination in pharmaceutical products, interacting with high-potency compounds and APIs, altering their chemistry and quality. In products like injectables, where it is not acceptable to contain any contaminants, dust particles can compromise patient safety.
Pharmaceutical manufacturing environments must adhere to strict air quality specifications outlined by regulations such as ISO 14644-1 and EU GMP Annex 1. Noncompliance can result in hefty fines, product recalls or even facility shutdowns, and any violations can cause significant damage to the brand.
Air filtration in cleanrooms and process dust collection solutions are crucial in ensuring the safety and quality of pharmaceutical manufacturing. They help meet health and safety regulations and enhance throughput by maintaining consistent product quality. As the generic drug market expands, pushing brand drug manufacturers to be more efficient and flexible, filtration systems can help reduce operating costs by lowering energy consumption and equipment downtime.
Camfil provides air filtration solutions for pharmaceutical manufacturing that use cutting-edge HEPA (high-efficiency particulate air) filters suitable for different areas within OSD facilities. Commercial air filters are typically less efficient than HEPA filters, which have a minimum particle capture efficiency of 99.97% on 0.3-micron particles.3
In the wake of global concerns over transmissible diseases, HEPA filters have gained even more significance as they can filter out numerous airborne fungal, bacterial and viral pathogens, including the SARS-CoV-2 virus responsible for COVID-19.
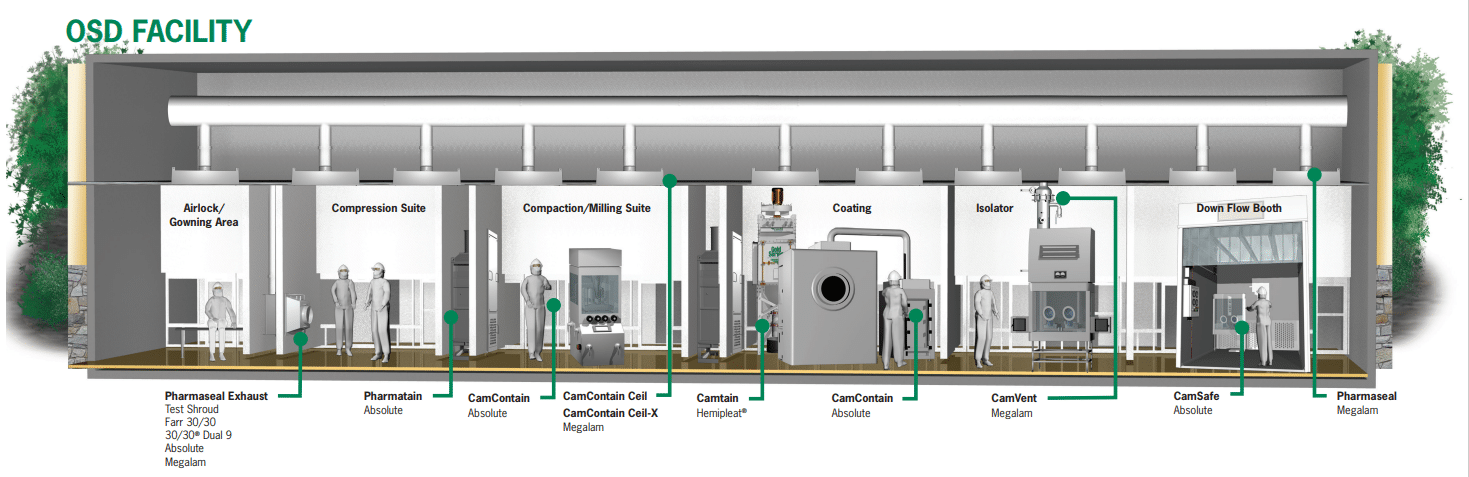
Camfil has HEPA (high-efficiency particulate air) filters suitable for these areas within OSD facilities.
Camfil HVAC solutions for pharmaceutical manufacturing include:
Area | Solution |
Air handling unit (AHU) for incoming/outdoor air or recirculated air | High-end prefiltration for minimizing total cost of ownership and protecting critical areas |
Milling, blending, formulating, compression suites and coating areas | HEPA filters and housing systems for reliable operations: Pharmaseal®, Pharmaslim® (for terminal air supply) and Pharmatain® (for exhaust air) |
Isolator areas,
downflow booths |
Megalam® HEPA and push-push filters, custom made for OEM, for work environment protection |
Conveying and loading areas | CamCleaner air purifier for maintaining a clean, safe warehouse |
Administrative offices | Quality AHU filtration to ensure employee well-being and productivity |
Camfil air filters offer many benefits including:
- Sustaining product quality by protecting processes from contamination and cross-contamination
- Reduction of product recalls and liability
- Protecting environments from potentially harmful air exhaust
- Protecting workers from interacting with potent compounds
- Compliance with strict regulations and supporting internal quality operating standards
- Minimizing operation costs with the most efficient and reliable filter, the heart of the filtration system
Aseptic Drug Processing
The manufacturing process for sterile and/or biologic drugs differs from the process for traditional pharmaceutical products, and consequently air filtration needs also vary. These drugs often come in liquid form, eventually being used as eye drops or injectables. Maintaining a clean and sterile environment remains a top priority.
Biological products differ from chemically synthesized drugs in that they consist of proteins, sugars or a mix of living substances such as cells and tissues. Examples of these biological products include gene therapy, tissues, blood components and somatic cells. Biologics are sensitive to heat and prone to contamination, so they must be sterilized using aseptic processing techniques under the strictest ISO 5 (Class 100) room standards.4
In contrast to sterile manufacturing, which applies heat to the end product to eliminate living microorganisms, aseptic pharmaceutical manufacturing ensures that no contamination is present from the creation of the components through to the packaging process. Aseptic processing is particularly useful when drugs cannot endure the heat cycles of terminal sterilization, which sterilizes a product in its final packaging form.5
Air filtration in aseptic manufacturing requires environments be filtered to achieve high air quality that is free from contaminants and bioburden. Camfil offers air filtration solutions for aseptic processing facilities in several different areas of the facility and stages of the process.
Medical Devices Manufacturing
Manufacturing medical devices also requires stringent cleanliness standards. Cleanrooms must comply with regulations for aseptic or controlled environments. Devices not terminally sterilized are manufactured in an aseptic environment that adheres to ISO 5 cleanroom standards.6 Devices that are terminally sterilized, meaning they are sealed in a package after sterilization, typically require an ISO 7 or 8 cleanroom environment.
Area | Solution |
Air handling unit (AHU) for
incoming outdoor air or recirculated air |
High-end prefiltration for minimizing total cost of ownership and protecting critical areas |
Cleanrooms, wash and prep | Efficient HEPA filters and housing systems for reliable operations– Pharmaseal®, Pharmaslim® (for terminal air supply) and Pharmatain® (for exhaust air) |
Depyrogenation tunnels and sterile preparation rooms | Absolute D-Pyro, the most efficient high-temperature filter on the market |
Aseptic filling, mini-environments like restricted access barrier systems (RABS) and isolators | Megalam® HEPA filters and push-push filters for work environment protection, custom made to fit OEM equipment |
Packing areas | CamCleaner air purifiers for maintaining a clean, safe warehouse |
Aseptic sections of the cleanrooms ensure minimal presence of microorganisms from the design to development stages by maintaining the highest possible sterility throughout the facility.
Camfil air filtration solutions for aseptic environments provide:
- Shielding of products from contamination and cross-contamination, ensuring product quality
- Reduction of product rejects and associated liabilities
- Prevention of accidental contact of employees with biological matter
- Protection of the environment by upholding appropriate biosafety levels
- Compliance with stringent environmental and workplace regulations
- Cost savings in pharmaceutical manufacturing through energy-efficient filter performance
- Easy and safe filter changes, causing minimal disruption to operations and eliminating risk of contamination
Molecular Air Filtration
Pharmaceutical products often use potent flavoring additives and hydrogen disulfide process gases, which can generate strong or unpleasant odors even at low concentrations. Some of these gases can harm a worker’s respiratory system. The smallest molecular pollutants can evade even the most effective HEPA and ULPA particle filters since gas molecules can be at least one thousand times smaller than dust particles.7
Camfil molecular air filters are designed to remove gases and vapors from the air using a technique called adsorption. These filters are sometimes referred to as chemical filters or gas-phase filters. The active ingredient in almost all Camfil molecular filters is either activated carbon or activated alumina.
Camfil offers a range of molecular filters, tailored to various process and application needs (see below). Sometimes, multiple stages of molecular filters are needed to capture different kinds of molecules within the same application. The selection of filters primarily depends on the types and concentrations of gases and the intended lifespan of the system. Many of these filters are used to supplement HVAC systems.
Camfil Molecular Filter Products
Concentrations | Solution |
Low concentrations of gases | Pleated, embedded media filters: CityPleat, CityCarb, CitySorb |
Moderate concentrations of gases | Thin bed loose-fill media filters: CamCarb CG cylinders, PG panels or VG modules –Available in GlidePack® housings –Available in CamCleaner air purifiers and air cleaners |
Heavy concentrations of gases | Deep bed loose-fill filters: ProCarb deep bed scrubbers |
Camfil has the industry experience and knowledge to help pharmaceutical plants maximize worker safety, meet emissions limits, maintain compliance and maximize efficiency and profitability.
Advantages of Camfil Air Filtration Solutions
Camfil aids the life sciences industry by developing high-efficiency air filtration solutions suitable for cleanrooms, production areas and laboratories. These solutions support the cost-effective and sterile production of pharmaceutical and medical products that adhere to international standards. Camfil’s high-efficiency prefiltration, HEPA filters and air filter housings ensure the highest level of purity by protecting sensitive equipment, processes and staff from airborne contaminants.
Camfil air filtration solutions assist pharmaceutical, biologic and medical device companies in meeting standard operating procedures and complying with the strictest regulations. As technology progresses within the life sciences, Camfil ensures dynamic and efficient air filtration for quality assurance.
Without air filters, pharmaceutical companies and device manufacturers would not be able to safely produce medical devices, vaccines, gene therapies, highly potent drugs and other crucial pharmaceutical and science products.
As companies in the life sciences sector seek ways to cut production-related costs, Camfil cleanroom air filtration and dust collection solutions help companies produce high-quality pharmaceutical products that comply with regulations.
The choice of filtration system hinges on the nature and size of airborne contaminants, as well as the process to manufacture the end product. Camfil can provide guidance on specific applications and requirements, whether it involves new drug development or a necessary process upgrade. Simply upgrading to a more efficient air filter can result in cleaner air and reduced energy costs.
#####
1Pharmaceutical Processing World (2023, April) https://www.pharmaceuticalprocessingworld.com/drug-recalls-2022-2023-contamination-sterility-concerns/
2Cleanroom Classifications, (2021, May) https://sicweb.com/blog/93-cleanroom-classifications#:~:text=A%20typical%20indoor%20air%20sample%20may%20contain%20anywhere,see%20objects%20less%20than%2050%20microns%20in%20size.
3What is a HEPA filter, United States Environmental Protection Agency, What is a HEPA filter? | US EPA
4Understanding the Basics of Sterile Manufacturing, Renaissance, (2022, August) Understanding the Basics of Sterile Manufacturing – Renaissance (renpharm.com)
5The current state of aseptic processing and fill-finish manufacturing, CRB, https://www.crbgroup.com/insights/pharmaceuticals/aseptic-processing
6Cleanrooms for Medical Device Manufacturing, Instant Cleanroom Solutions, https://www.cleanroomsolutions.com/industries/medical-device-manufacturing#:~:text=Cleanrooms%20are%20used%20in%20the%20medical%20device%20manufacturing,sterilization%2C%20and%20quality%20control%20testing%20of%20medical%20devices.
7Molecular Filters, Camfil HVAC, Molecular filters | Camfil