According to the International Bottled Water Association,[1] bottled water has become the most popular beverage in America, with its consumption volumes increasing every year since 1997.[2]
Increasing health consciousness among consumers has also led to a rise in demand for organic beverages that are perceived to contribute positively to health. Market analysis by Mordor Intelligence forecasts that the organic drinks market will grow from $47.84 billion in 2023 to a staggering $60.00 billion in 2028.[3]
Many consumers view bottled beverages as a cleaner and safer choice. To ensure product quality and protect their brands, beverage manufacturers must ensure high air quality during production. However, standard heating, ventilation, and air conditioning (HVAC) systems often fail to remove all airborne particles effectively in production areas and other critical parts of a beverage facility.
The problem often lies in having the wrong filters . . . filters that cannot effectively remove contaminants from the air. In such cases, it is crucial to have a dedicated air filtration system with the appropriate filter to prevent possible contamination, safeguard the health of employees, and maintain the quality of the products.
This article will delve into the various types of contaminants, how they impact beverage production, and the critical role that air filtration products play in eliminating them.
Understanding Contaminants in Beverage Production
One of the processing methods that may be used in the beverage industry, depending on the beverage, is aseptic processing. Product is filled into sterilized containers and then hermetically sealed with a sterilized closure. Environments must be free of contaminants that can compromise the quality of the final product. The most harmful air contaminants are:
- Dust and Particulate Matter
These tiny airborne particles, like dirt and bacterial spores, can infiltrate open beverage containers during production or settle on the packaged products. The process of packaging finished beverage bottles for shipping can generate dirt particles that must be prevented from migrating to the more sensitive areas of the plant such as the filling areas. This is especially true when cardboard is used in packaging. Furthermore, these particles can interfere with machinery efficiency. Inadequate air filtration often leads to this form of contamination.
- Microorganisms and Bacteria
Facilities with poor sanitation or high moisture levels can foster microbial contamination and mold. This form of contamination often stems from poor moisture controls in rooftop air handling units or improper handling of products by workers who are not using protective gear or practicing good hygiene. If airborne bacteria and mold are not eliminated through robust air filtration, beverage purity can be compromised. These biological contaminants pose health risks to humans, including gastrointestinal illnesses and potential lung disease for employees if inhaled.
- Volatile Organic Compounds (VOCs)
These compounds, both naturally occurring and synthetic, contain hydrocarbons that can evaporate into the air and dissolve upon contact with water. HPV (hydrogen peroxide vapor) or PAA (peracetic acid) used as production equipment disinfectants are also common concerns.
Exposure to these VOCs can lead to health concerns for workers, including eye and nasal irritations and difficulty in breathing. Effective removal of VOCs from the environment requires air ventilation and molecular filtration that is capable of capturing s these gaseous irritants from the air.
Controlling Airborne Contaminants in Different Stages of Beverage Production
Contamination can occur during beverage production due to poor air quality in critical process areas. To minimize potential hazards to workers, equipment and the end product, bottlers should implement air filtration measures at these vital stages of beverage production.
Fermentation Process
The fermentation of beverages like beer, kombucha and wine involves chemical breakdown by bacteria and yeast. Compressed air introduces oxygen into yeast cultures. Therefore, filtering the process air is essential to produce sterile oxygen that is free of particulates and moisture. This filtration ensures the highest-quality beverages that meet both safety and consumer standards.
Bottling Process
In the beverage industry, aseptic processing and packaging methods require an environment devoid of microorganisms to reduce the risk of contaminating the product. There should be no organisms present during the filling and capping stages of the production lines.
Many facilities use compressed air to drive bottling lines and clean equipment and containers. The intake air must be free of contaminants like particulates and oil mist generated from the compressor. Using air filtration systems can assure the purity of air, especially in direct contact applications.
Air conveyor fans blow empty bottles on overhead tracks from station to station as they are prepared for filling. These fans can force contaminants deep into the empty bottles before filling, so air from these fans must be filtered to reduce this possibility and to improve the sterilization process.
Storage Facilities
Often, finished beverage products are stored in air-conditioned areas to preserve their quality. Even the most efficient air conditioning systems can discharge bacteria into the environment. Air conditioning systems with inadequate filtration can circulate up to 15 million bacteria each hour, compromising product quality.[4]
Using air filtration systems in these facilities can prevent contaminants from settling on goods or being inhaled by workers, thus safeguarding both from harmful effects.
Advantages of High-Quality Air Filters for Beverage Production
The role of air quality in beverage production is critical for several reasons, making it an important component of successful operations.
Maintaining Product Quality and Safety
Poor air quality can produce unwanted results in beverages and cause early product spoilage. Pathogens in the air, VOCs and other contaminants can pose a threat to worker safety. Using effective air filters can mitigate microbiological contaminants during aseptic processes, maintaining product quality and protecting workers’ health.
Compliance with Industry Regulations and Standards
Governments around the world regulate food and beverage production to minimize contamination risks in food and beverage production facilities. For instance, the U.S. Food & Drug Administration (FDA) mandates Current Good Manufacturing Practices for bottled water manufacturers to protect water sources from bacteria, chemicals and other contaminants. The FDA also enforces strict guidelines for aseptic processing and packaging in a microbe-free atmosphere.[5]
Organizations such as IFTPS (Institute for Thermal Processing Specialists) provide education and training for those working in certain critical food processing fields. Furthermore, international standards like ISO 22000 outline the safety requirements for food production. Air filtration systems play a vital role in enhancing air purity in various beverage production processes, ensuring compliance with clean environment requirements and protocols that enhance worker safety and product quality.
Promoting Energy Efficiency and Cost Savings
Energy-efficient air filters reduce energy consumption, leading to cost savings. When filters perform with lower airflow resistance, the air handling system does not have to work as hard, reducing energy use and related costs.
Improved Airflow and Lower Maintenance Costs
Inferior air filters often need frequent replacements due to failures, which can lead to system contamination, production loss and recurrent maintenance issues, such as continually adjusting line airflows. These failures also incur additional costs in materials and labor.
High-quality air filters optimized for a specific application have a longer service life, so they are replaced less often, reducing labor and waste costs. Because these filters perform optimally, they increase resistance more slowly, eliminating the need to adjust line airflow. The resulting operational efficiency reduces production downtime and losses.
Enhancing Equipment Longevity and Reliability
Poor air filtration can allow particles to infiltrate equipment, causing wear and tear that leads to reduced efficiency or breakdowns. Uncaptured particulates can clog equipment, restricting the flow of fluids, which decreases performance while increasing energy consumption. By removing airborne particles and chemical impurities from the production environment, the equipment remains reliable for long-term operations, ensuring consistent production.
Boosting Brand Reputation and Consumer Confidence
Effective air filtration prevents contamination during production processes, ensuring the finished product’s consistent taste and quality. Contaminants such as dirt and bacteria can alter or diminish a product’s taste or even cause spoilage. Delivering a consistent product not only enhances customer experience but also strengthens brand reputation.
Types of Air Filters for Beverage Production
Air filters are available in different categories that address specific air filtration requirements.
General Ventilation Filters
These are high-quality and energy-saving general ventilation filters that help protect workers, processes and products from particulate matter. They are used in HVAC applications as the final filter for comfort applications, prefilters in clean process applications, or exhaust air or recirculation systems to protect air handling units. General ventilation filters come in several designs including bag filters, V-shaped header frame filters and pleated panels. Each has its role in different filter stages in the air supply.
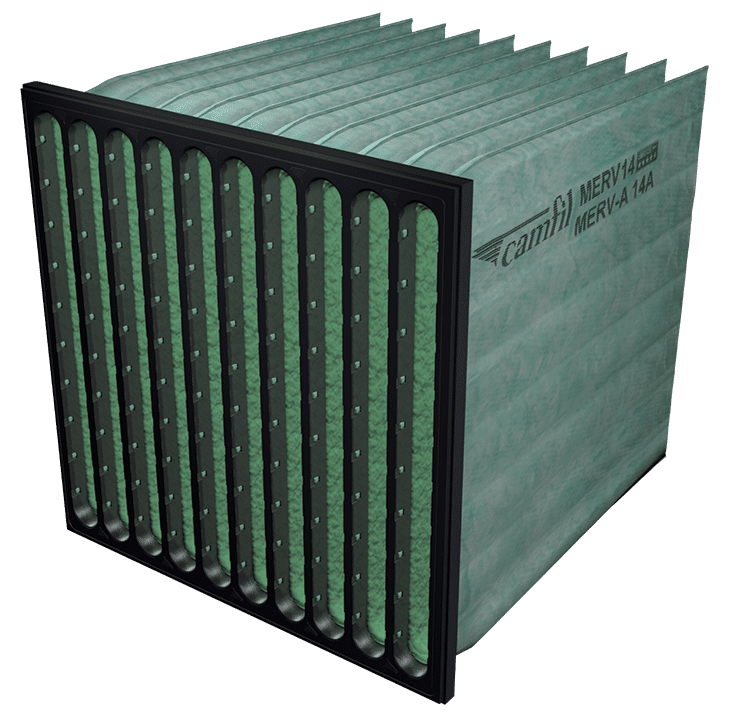
This Camfil Hi-Flo ES bag filter is used in HVAC applications as a high-efficiency filter or as a prefilter in high-efficiency particulate air (HEPA) installations.
High-Temperature Filters
Engineered to protect ultra-clean processes at elevated temperatures, these filters retain their integrity and rated performance at temperatures up to 650 °F (350 °C). They are used in food and beverage operations, as well as in the automotive and pharmaceutical industries, complying with the strict FDA GMP requirements.
High-Efficiency Particulate Air (HEPA) and Ultra-Low Particulate Air (ULPA) Filters
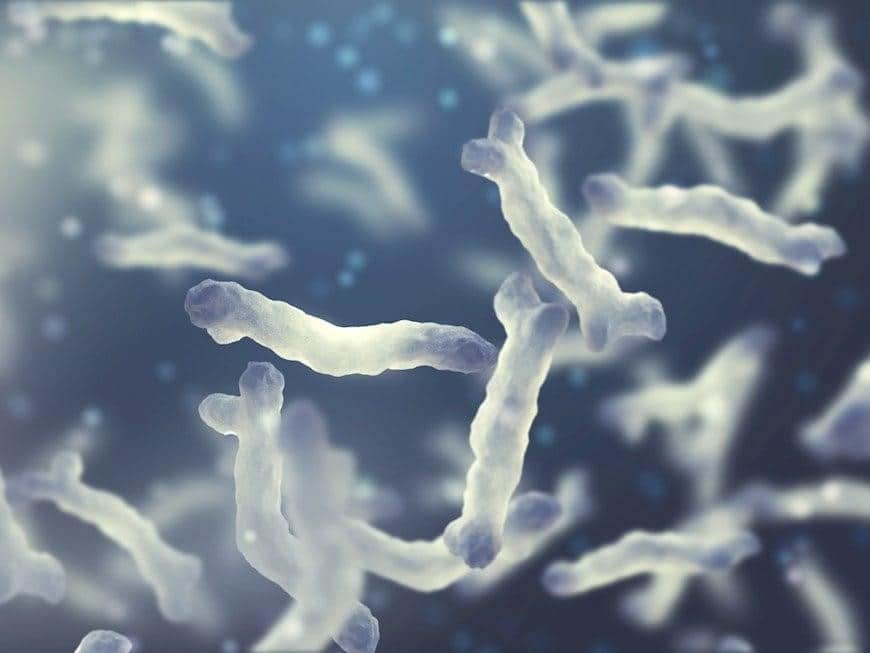
Particles captured by a HEPA ULPA Filter
HEPA and ULPA filters are used in sensitive advanced manufacturing processes to prevent microbiological contamination. These filters are components within air filtration systems or integral components of individual filling and packaging systems, and they work to eliminate microbial contamination in beverage facilities.
Ideal for industries with stringent quality requirements, these filters improve product integrity while minimizing financial risks. There are three major global classification standards for HEPA and ULPA filters. While the test standards differ slightly, the minimum definition of a HEPA filter is generally a filter tested to remove at least 99.97% of particles 0.3-microns or larger, which is about 300 times smaller than a human hair.[6] HEPA filter classification can go as high as 99.995% efficiency. ULPA classification begins where HEPA ends and can go as high as 99.999995% on MPPS, the most penetrating particle size.
Molecular Air Filters
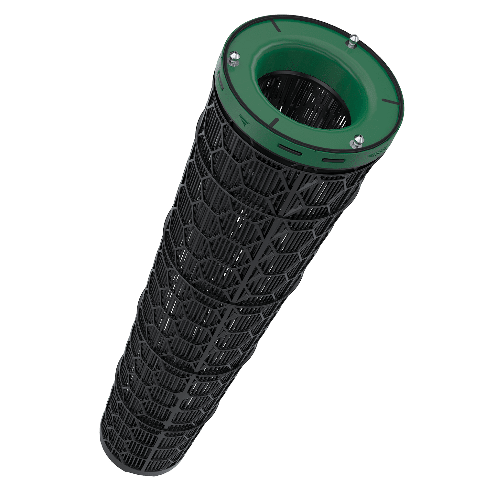
This CamCarb cylindrical molecular filter removes gaseous contaminants from supply, recirculation and exhaust air applications. The filters can be filled with activated carbon to provide broad-spectrum or impregnated carbon or alumina for targeted adsorption of contaminants such as odors, irritants, and toxic and corrosive gases and vapors.
Airborne VOCs and disinfection product off-gases can pose problems, causing unpleasant odors and adverse health effects such as respiratory illnesses. Besides removing airborne particles, filtration solutions for beverage production environments should also remove these gaseous compounds.
Molecular filters, also known as chemical, carbon or gas-phase filters, eliminate gases and vapors from the air using the process of adsorption. Molecules adhere to or react with adsorbent filter materials with extremely high surface areas.
Molecular air filters use activated carbon for broad-spectrum VOC removal or chemically impregnated carbon or alumina for targeted removal of specific gases. Multiple stages of molecular filters might be necessary to capture different types of gases in the same application.
Selecting the Appropriate Air Filter
Air filters play a crucial role in maintaining clean air across a beverage facility. Here are the suggested filters for various areas.
High-Care Areas
High-care areas need air filters that minimize contamination before it reaches high-hygiene zones, thus protecting equipment. Potential threats in this region may include bacteria, corrosive gases, disinfectants, dust, mold spores, nanoparticles, water droplets and VOCs.
Recommended Air Filters:
- HEPA and ULPA filters
- Molecular air filters
Medium-Care Areas
These are usually areas where raw materials are stored, including packaging, warehousing and plant entrances. Potential issues include agricultural contaminants, bacteria, combustion particles, corrosive gases, disinfection and sterilization agents, dust, grease, mold spores, pollen, coarse particles, oil mist and others.
Recommended Air Filters:
- General ventilation filters
- HEPA and ULPA filters
- Molecular air filters
Low-Care Areas
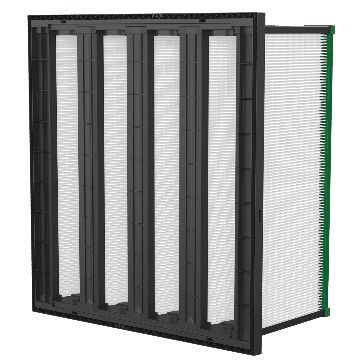
Camfil’s Durafil ES filter is a highly efficient filter available in MERV 11A, 13A, 14A and 16A efficiency ratings.
These areas are outside of production and product handling and prioritize the health of building occupants. Potential issues include offensive
odors, bacteria, allergens, corrosive gases, dust, mold spores, nanoparticles, pollen, viruses, VOCs and water droplets.
Recommended Air Filters:
- General ventilation filters
- Molecular air filters
High-Hygiene Areas
During final product processing and packaging, the environment must uphold the highest hygiene levels. Filters should provide the best air
quality by eliminating all contaminants during aseptic filling. Potential concerns include bacteria, combustion particles, mold spores, nanoparticles, coarse particles, pollen and viruses.
Recommended Air Filters
- HEPA and ULPA filters
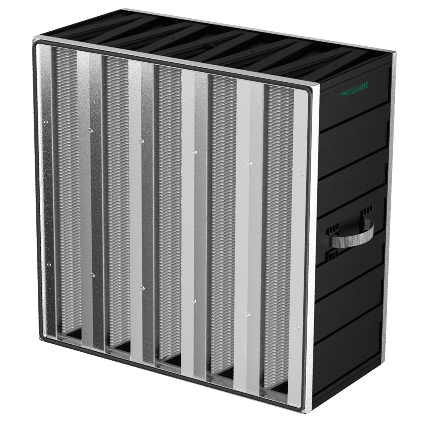
This Camfil Absolute VG HEPA filter provides 99.99% efficiency at 0.3 microns.
The correct specification of an air filtration system can ensure the protection of both processes and personnel in beverage production facilities. The result is improved working conditions and a consistent, high-quality product that elevates the customer experience and enhances brand image.
The air filter choice depends on the specific contaminants of concern and their efficiency in capturing particulate matter or other airborne contaminants over time. Understanding the different types of air filters and MERV ratings is essential to choosing the right filter for a specific air filtration application. As discussed earlier, certain filters are best suited for high-temperature environments or sensitive manufacturing processes, while others are designed to capture airborne particles of specific sizes or various gaseous compounds.
Consulting with an air filtration expert with experience in the beverage industry and knowledge of the latest air filtration technology is the best approach to get an optimum solution. They can conduct an audit of a beverage production facility and outline an air filtration strategy that meets specific requirements.
Investing in air filtration yields dividends in improved personnel health and performance, increased productivity, longer equipment lifespan, reduced waste and downtime, and consistent product output.
[1] Consumer thirst for bottled water is stronger than ever, survey finds, October 11, 2022, International Bottled Water Association, https://www.globenewswire.com/en/news-release/2022/10/11/2531883/0/en/Consumer-thirst-for-bottled-water-is-stronger-than-ever-survey-finds.html.
[2] Bottled Water 2020: Continued Upward Movement U.S. and International Developments and Statistics, JUL/AUG 2021, Bottled Water Reporter, https://bottledwater.org/wp-content/uploads/2021/07/2020BWstats_BMC_pub2021BWR.pdf.
[3] Organic Beverage Market Size & Share Analysis – Growth Trends & Forecasts (2023 – 2028), Mordor Intelligence, https://www.mordorintelligence.com/industry-reports/organic-beverage-market#.
[4] How Ventilation Affects Air Quality at Food Processing Plants, Camfil Air Filters, June 2, 2020, https://cleanair.camfil.us/2020/06/02/ventilation-affects-air-quality-food-processing-plants/.
[5] FDA Regulates the Safety of Bottled Water Beverages Including Flavored Water and Nutrient-Added Water Beverages, September 22, 2018, https://www.fda.gov/food/buy-store-serve-safe-food/fda-regulates-safety-bottled-water-beverages-including-flavored-water-and-nutrient-added-water.
[6] HEPA/ULPA FILTERS, Camfil Air Filters, https://catalog.camfil.us/hepaulpa-filters.html.